Главная → Примеры внедрения → НПП "МЕРА" – передовые решения для стенда статических испытаний
НПП "МЕРА" – передовые решения для стенда статических испытаний
При создании новейших образцов авиационной техники повышенное внимание уделяется оптимизации используемых компонентов, конструкционных материалов, конструкторских решений. При этом одним из важнейших видов испытаний был и остаётся анализ напряжённо-деформированного состояния конструктивных элементов для согласования результатов испытаний с расчётными значениями. До настоящего времени в большинстве эксплуатируемых стендов статических испытаний в качестве силовозбудителей применяются системы, построенные на гидравлическом или пневматическом принципе передачи усилия. В 2013 году НПП «МЕРА» ввело в эксплуатацию систему статических испытаний, в которой заложено принципиально иное решение по созданию нагружающего усилия – электромеханические силовозбудители.
Рис. 1. Статические испытания имитатора двигателя ПД-14
(источник фото: ИТБ «Пермские авиационные двигатели» № 28, июль 2013 г.)
Задача
Создание системы нагружения и управления и системы измерений специализированного стенда статических испытаний двигателя ПД-14 и крупногабаритных узлов из полимерных композитных материалов.
Рис. 2. Эскиз стенда статических испытаний
По условиям технического задания схема должна включать в себя следующие виды нагружения: вертикальное, боковое, осевое, крутящие моменты. Эти нагрузки должны производиться системой силовозбудителей, развивающих усилия до 40 тонн. Погрешность задания усилия не должна превышать ± 1% от номинальной величины силовозбудителя. Важным условием является жёсткость испытываемого объекта (более 15 тонн/см), что подразумевает высокую точность позиционирования силовозбудителей. Поскольку одновременно к объекту прилагается воздействие нескольких силовозбудителей, немаловажным фактором становится сведение к минимуму их взаимовлияния в процессе задания нагрузки. Таким образом, для решения поставленной задачи была необходима система, обладающая высокой скоростью реакции, точностью позиционирования и возможностью гибко настраивать профили нагружений.
В этих условиях перед разработчиками стояла проблема выбора нагружающих элементов системы. Рассмотрим те аргументы, благодаря которым были выбраны электромеханические цилиндры, принимая во внимание технические характеристики, показатели надёжности и стоимость.
Рис. 3. Электроцилиндр на базе планетарной ролико-винтовой передачи
Гидравлика, при всех своих достоинствах, требует для эксплуатации целого комплекса дополнительного оборудования (масляные баки и насосы, системы фильтрации масла, радиаторы для охлаждения, распределители и шланги для подачи и возврата рабочей жидкости, дроссели, клапаны, датчики, фитинги, втулки и уплотнения, поддоны), в то время как для работы электроцилиндров необходимы только силовой и сигнальный кабели и блок управления.
Если говорить о самом рабочем теле, гидравлической жидкости, то тут существуют и проблемы экологического характера: токсичность, загрязнение рабочего пространства испытательного бокса, пожароопасность. Утечки жидкости вследствие износа прокладок снижают точность позиционирования, по этой же причине не гарантирована повторяемость, т. е. наличие одного и того же усилия. Большой комплекс дополнительного оборудования, необходимость замены прокладок и уплотнений приводят к существенным расходам на обслуживание системы гидравлических силовозбудителей. Электроцилиндры обладают большим сроком службы и практически не требуют технического обслуживания. При работе 8 часов в день замена смазки может производиться раз в три года. Из-за дополнительного оборудования системы на базе гидроцилиндров занимают значительно больше места, чем электромеханические системы, хотя сами гидроцилиндры компактнее электроцилиндров.
Электромеханика способна развивать ускорения до 100 м/с2 в прямом и обратном направлении, что позволяет осуществлять точные высокоскоростные реверсивные движения. Динамические показатели гидравлических систем значительно уступают этим характеристикам. При высоких скоростях работы и значительных развиваемых усилиях точность позиционирования электромеханических цилиндров может не превышать нескольких микрон. Электроцилиндры способны работать на скоростях до 1,5 м/сек с усилиями до 400 кН, имеют ход штока до 1,2 метров с точностью позиционирования порядка одного микрона.
В случае применения электроцилиндров легче решаются задачи управления усилием и позиционирования. Поскольку работать приходится с электрическим напряжением, а не с жидкостями, значительно упрощается программирование профиля нагрузки. Расходы на обеспечение электроэнергией у гидравлических силовозбудителей также оказываются выше, чем у электромеханических. КПД электроцилиндров более 85%, а потребляемый ток изменяется пропорционально развиваемой нагрузке. Кроме того, при отсутствии изменения нагрузки потребление можно свести до минимума за счет использования электромагнитного тормоза, удерживающего заданное усилие в требуемом положении.
Сравнительная таблица электромеханических и гидравлических силовозбудителей
Показатель |
Электромеханика |
Гидравлика |
Номинальная нагрузка |
Высокая |
Очень высокая |
Дополнительные компоненты |
Силовой и сигнальный кабели и блок управления |
Насосы, резервуары, фильтры, клапана, радиаторы и т. д. |
Динамические показатели |
Высокие |
Низкие или средние |
Использование при низких температурах |
Не требует дополнительного оборудования |
Требуется подогрев масла |
Стоимость монтажных работ |
Низкая |
Высокая (требуется установка гидравлических линий, сервоклапанов, маслостанции и т. д.) |
Интервалы обслуживания |
Очень длинные |
Короткие |
Требуемое обслуживание |
Редкая смазка подшипников |
Проверка и замена масла, проверка на протечки, замена фильтров |
КПД |
> 80 % |
< 50 % |
Пожаробезопасность |
Хорошая |
Только при использовании жидкостей на водной основе |
Сложность точного управления |
Незначительная |
Высокая (из-за качества масла, температуры, давления) |
Точность (относительного полного хода штока) |
Незначительное отклонение |
Значительно зависит от скорости (возможно на низкой скорости) |
Распределение усилия |
Одинаковое |
Значительно возрастает в конечных положениях |
Несомненно, системы на основе гидравлических силовозбудителей могут обладать некоторыми преимуществами. Гидравлические цилиндры дешевле, чем электромеханические системы. При использовании большого количества гидроцилиндров на небольшом участке, когда стоимость дополнительного оборудования распределяется пропорционально на все цилиндры, их применение может оказаться более целесообразным. Они также могут развивать очень большие усилия. В рассматриваемом нами случае преимущества электроцилиндров оказались весомее, а потому в качестве силовозбудителей специалистами НПП «МЕРА» были применены электромеханические цилиндры.
Возвращаясь к техническим требованиям на систему нагружения, стоит отметить, что важным пунктом было требование отработки на программном и аппаратном уровнях аварийных режимов и ситуаций на объекте испытаний и системах стенда, а также требование по обеспечению безопасности персонала. Система должна предусматривать возможность аварийной разгрузки в автоматическом и ручном режимах в случаях достижения критической уставки, срабатывания ограничительного концевика, отсутствия напряжения на одном из цилиндров и т. д.
Решение
Система нагружения
Система нагружения стенда статических испытаний обеспечивает задаваемое программой испытаний силовое воздействие на конструкцию испытываемого объекта, контроль и управление процессом нагружения, контроль параметров нагружения и передачу их значений в измерительную систему.
Не считая точек крепления конструкции объекта испытаний, система нагружения обеспечивает силовое воздействие на объект, создавая в соответствии с программой растягивающие, сжимающие, изгибающие или крутящие усилия.
Рис. 4. Подготовка системы нагружения стенда к испытаниям
Структурно система нагружения разделяется на элементы нагружения объекта испытаний и подсистему управления нагружением. Элементы нагружения – электроцилиндры различного номинала. Подсистема управления нагружением включает в себя:
- частотные преобразователи;
- процессорный и измерительные модули на базе сети реального времени EtherCAT;
- тензорезисторные S-образные датчики сжатия-растяжения;
- промышленный компьютер и сетевое оборудование;
- ПО настройки режимов и контроля управления нагрузкой.
В соответствии с программой испытаний изделия параметры нагружения вводятся в ПО, установленное на управляющем компьютере. Информация о величине усилий, которые должен создать каждый электроцилиндр, по Ethernet передается в процессорный модуль. Процессорный модуль по сети EtherCAT передает команды управления электроцилиндрами на частотные преобразователи. Каждый частотный преобразователь формирует питающее напряжение для подключенного к нему электроцилиндра.
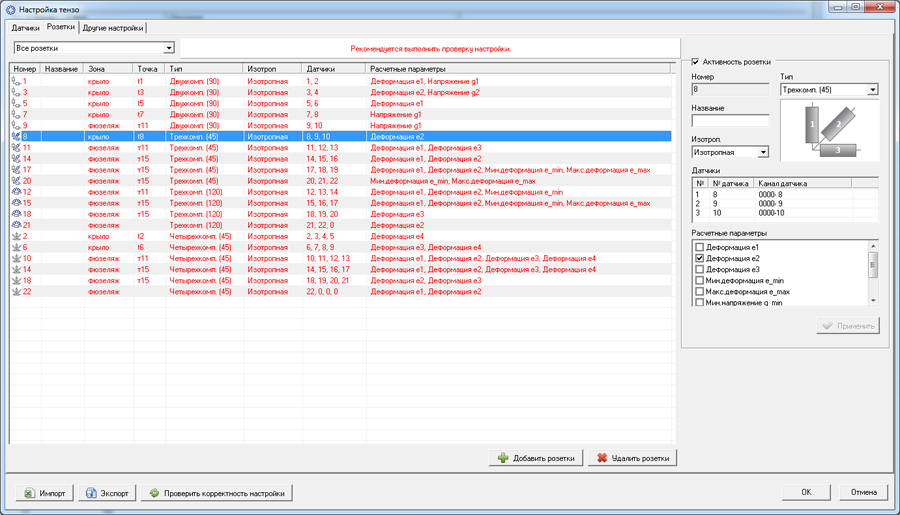
Рис. 6. «Нагружение» – программное обеспечение настройки циклограмм управления нагружением
Рис. 7. Структурная схема системы нагружения
В начале цепи обратной связи системы нагружения находятся тензорезисторные S-образные датчики сжатия-растяжения, установленные между штоком электроцилиндра и объектом испытаний. Возникающее на них напряжение, пропорциональное приложенному усилию, поступает на входы модуля ввода/вывода, где сигнал обрабатывается и передаётся в процессорный модуль и далее на частотные преобразователи. Информация о реальной величине усилий на штоках электроцилиндров позволяет обеспечить высокую точность нагружения.
На корпусах электроцилиндров установлены концевые выключатели, определяющие границы перемещения штоков. Концевые выключатели подключены к схемам управления сервомоторами, и обеспечивают отключение питания электроцилиндра при достижении предельных положений штоков.
Рис. 8. Сборка шкафов управления
На дверцы шкафов управления выведены панели ручного управления положениями штоков электроцилиндров, необходимые для начальной установки штоков при монтаже элементов нагружения.
Рис. 9. Шкафы управления
Шкафы управления, разработанные специально для оборудования стенда нагружения, содержат:
- частотные преобразователи;
- силовые шины питания и электрическую обвязку (дроссели, реле, автоматы, моторные приводы, разъединители с предохранителями и т. д.) для стабильной работы частотных преобразователей;
- блок автоматических выключателей для коммутации и защиты цепей системы нагружения;
- панели ручного управления и индикации;
- вентиляторы охлаждения.
Подводка кабелей к шкафам выполнена в кабельных каналах, расположенных под фальшполом.
Система измерений
Система измерений стенда статических испытаний предназначена для измерения и регистрации различных параметров в процессе проведения испытаний:
- параметров статического нагружения объекта испытаний, в том числе прикладываемых усилий;
- деформаций и перемещений нагружаемых узлов и деталей;
- механических напряжений элементов конструкции и деталей объекта испытаний.
Система измерений стенда осуществляет автоматизированный сбор, регистрацию, обработку и визуальное представление данных. Она обеспечивает измерение статических деформаций по 1024 каналам, а также измерение абсолютных и относительных перемещений по 43 каналам. Измерение относительного напряжения тензорезисторов по полумостовой и мостовой схемам осуществляется с пределом основной приведённой погрешности ±0,05 %. Погрешность измерения перемещений не превышает ±0,3 % от измеряемой величины. Диапазон измерения перемещений не более 25 мм.
В ходе измерений предусматривается возможность наблюдения значений измеряемых параметров в реальном масштабе времени на семи рабочих местах операторов.
При математической обработке имеется возможность расчёта нормальных и касательных напряжений по показаниям как одиночных тензорезисторов, так и тензорозеток (двух- или трёхэлементных). Выдача данных производится в табличной или графической форме. Возможно проведение линейного сглаживания и аппроксимации эмпирических данных по каждому измерительному каналу.
Система измерений стенда включает:
- подсистему измерения напряжений и деформаций;
- подсистему измерения линейных перемещений контактными датчиками;
- подсистему измерения линейных перемещений лазерную триангуляционную;
- подсистему измерения усилий, прикладываемых к объекту испытаний;
- систему видеорегистрации событий, происходящих на объекте и в зоне стенда в процессе подготовки и проведения испытаний.
Основные технические характеристики системы измерений
Параметр |
Значение |
Количество каналов измерения деформации тензорезисторами, штук |
1024 |
Количество каналов измерения перемещений контактными датчиками, штук |
20 |
Количество каналов измерения перемещений лазерными триангуляционными датчиками, штук |
23 |
Количество каналов измерения усилия, штук |
25 |
Диапазон изменения напряжения тензорезисторов, мВ (при напряжении питания моста 2,5 В) |
±5,0 … ±20 |
Диапазоны измерения деформаций, мкм/м (με) |
±4000 ±16000 |
Диапазон измерения перемещений, мм |
0 … 25 |
Диапазон измерения усилия, кгс |
0 … 50000 |
Частота дискретизации каналов измерения перемещений, Гц |
5 |
Частота дискретизации каналов измерения напряжения тензорезисторов, Гц/канал |
6 … 1024 |
Частота дискретизации каналов измерения усилия, Гц |
100 |
Питание тензорезисторов, В |
2,5; 5 |
Рабочий диапазон сопротивление тензорезисторов, Ом |
100 … 1000 |
Пределы основной приведённой погрешности измерения напряжения тензорезисторов, % |
±0,3 |
Пределы основной приведённой погрешности измерения линейных перемещений, % |
±0,5 |
Пределы основной приведённой погрешности измерения усилия, % |
±0,5 |
Напряжения тензодатчиков по 128 групповым кабелям поступают на входы 256-ти четырехканальных измерительных модулей типа MR-212, входящих в состав 16-ти многоканальных измерительных комплексов MIC-236. Часть кабельных каналов и слотов комплексов MIC-236 задействована под модули MR-114, MR-114С1, MR-405 и MR-406, которые используются в технологических целях специалистами-изготовителями системы измерений при её настройке и эксплуатации.
Рис. 10. Приборные стойки с MIC-236 и станциями единого времени ME-020 для приведения к единому времени 1024 тензоканалов модулей MR-212.
На первом плане стойка с рабочими станциями для сбора, хранения, обработки и отображения информации.
Комплексы MIC-236 установлены в три приборные 19" стойки. В этих же стойках размещены модули синхронизации МЕ-020В8, обеспечивающие синхронность работы всех измерительных модулей и комплексов, установленных в стойку.
Рис. 11. Структурная схема системы измерений
В четвертую приборную стойку установлены 8 промышленных компьютеров, задействованных в системе управления нагружением стенда, в системе сбора данных, видеорегистрации, а также для обработки и отображения измерительной информации на рабочих местах операторов.
В каждой стойке установлены сетевые коммутаторы, объединяющие все устройства системы управления нагружением и системы измерения в локальную сеть, а также обеспечивающие передачу информации в локальную сеть предприятия.
Все стойки оснащены источниками бесперебойного питания, обеспечивающими сетевым напряжением 220 В частотой 50 Гц размещенные в стойках устройства.
Автоматизированные рабочие места операторов системы находятся на расстоянии 20 м от измерительной аппаратуры в специально оборудованном помещении, оснащенном 14-тью видеомониторами, два из которых плазменные панели. Управление станциями сбора данных осуществляется с рабочих мест операторов посредством активных удлинителей шины USB.
Рис. 12. Структурная схема потоков информации в системе измерений
Для управления системой измерений стенда и подсистемой видеорегистрации используется ПО Recorder, дополненное обеспечивающим работу отдельных устройств системы измерений программным модулем «Тензо» (ПО определения характеристик жёсткости конструкции).
Обработка полученных в ходе испытаний данных производится средствами пакета обработки сигналов WinПОС Professional.
Всё программное обеспечение систем управления нагружением, измерений и обработки данных было настроено для обеспечения типовых процессов испытаний авиационных двигателей.
Рис. 13. Формуляр отображения программного обеспечения системы измерений в процессе испытаний
Измерительная система специализированного стенда для проведения сертификационных статических испытаний двигателя ПД-14 ОАО «Авиадвигатель» внесена в госреестр средств измерений под номером № 54735-13.